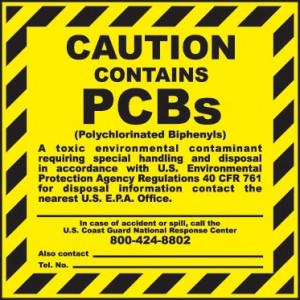
Managing PCBs In Your Building
How to avoid exposure
Interview with Tim Falling, COO/Vice President, Mark Sanchez, Vice President and Ian Sutherland, Staff Geologist
Q. What is PCB and what is it used for?
A: Polychlorinated Biphenyls are part of a broad family of man-made organic chemicals known as chlorinated hydrocarbons. PCBs were manufactured from 1929 until banned in 1979. PCBs have a range of toxicity and vary in consistency from thin, light-colored liquids to yellow or black waxy solids.
Q. What are the common products and materials that I may have at my building that still contain PCBs?
A: Caulking, electrical components, florescent light fixture ballasts, insulated coolant (transformers), as well as many paints can have PCBs. It also can be found in adhesives or any type of coating. PCBs are especially present in older buildings (50s through 70s).
Check out the EPA for a complete list of PCB containing materials.
Q. Do PCB containing materials pose a risk to tenants, employees or vendors that work in the building? If so, what are the risks and in what circumstances would there be an issue?
A: Yes, one example of a risk is Inhalation and Ingestion Exposure Routes:
PCBs are added to product to help maintain flexibility but these products are subject to wear and will breakdown over time. If people touch these materials and then eat without washing their hands, they may be exposed. Dust from renovations, repairs, and maintenance work may contain PCBs and can cause exposure if not properly identified and controlled.
Another is Bio-accumulation:
PCBs move their way up the food chain through accumulation in plants and animals. When ingested they don’t break down so if you consume food contaminated with PCBs the contamination spreads– in Japan there have been studies linking PCB contaminated fish to human birth defects.
For more information on health effects visit the EPA
Q. What population is at risk in a commercial building and am I required to notify them of the presence of these materials?
A: No notification requirements exist yet pertaining to tenants or employees, etc., but, the EPA reviews waste manifests and may question means and methods if they see PCB waste on a manifest. Currently, the EPA does have guidelines that offer approaches for how to manage PCB’s. There is a growing awareness among building owners and many are taking a more pro-active approach to identifying and managing PCB waste. This trend is especially prevalent on the East Coast. More commercial buildings are electing to test and remove PCBs when testing for other hazardous materials.
Q. How do I manage PCB exposure in a renovation/ construction/ demolition project if the material is going to be disturbed?
A: First sample materials suspected to contain PCB, if they contain hazardous material establish handing & disposal procedures and then remove it safely.
In a recent demolition project ACC learned a lot about working with the EPA and their direct oversight methods. The building was filled with caulking from the mid-60s that our testing showed contained 50-60,000 parts per million. Once identified our focus was the complete removal of the caulking as well as impacted concrete in contact with the caulking and ultimately soils near the drip line of the building that were also affected.
There are some defined abatement options in the EPA guidelines. Although for materials that are going to be recycled there are no guidelines, so, our project team performed a pilot study to ensure our abatement methods met the EPA’s stringent guidelines.
The Abatement Plan
The affected materials coated with PCB containing caulk were both porous (concrete) and non-porous (metal and glass). the Pilot Study determined that PCB contamination had penetrated up to four inches into the porous concrete in contact with PCB caulking. ACC, in close consult with the EPA, created a work plan to guide the contractor’s activities that included means and methods to remove the PCB caulk from the materials, cleaning of the non-porous materials and removal of contaminated porous materials to allow for demolition and re-cycling of concrete and metal.
Soil Contamination
Due to the concentrations in the caulking there was a concern that the PCBs ran into the soil and again ACC worked with the EPA to determine remediation goals. We sampled exposed soils around the building within 1-4 feet out from the foundation and then beneath the surface at varying depths; this resulted in finding PCB concentrations above the EPA established criteria in some locations prompting excavation of the soil to a depth where no contaminate was detected.
Q. Can any contractor remove or clean up – PCB containing Materials or spills?
A: Cal/OSHA has training requirements (e.g. 40 Hr. HAZWOPER or similar training) to protect workers during the handling of hazardous materials. Training also includes proper documentation of air sampling and proper tools used, etc….
For more information on Cal/OSHA training visit their website.
Q. Are there laws and regulations that I should be aware of that require me to discover if I have PCB’s materials at my building for management purposes or for renovation/demolition?
A: There are requirements to identify Hazardous Materials in general. PCBs are included in those requirements but there aren’t specific regulations yet, only guidelines set by the US EPA, however, once identified you’re required to deal with the material if the concentration is equal to or higher than 50 mg/kg.
PCBs are governed under The Toxic Substance Control Act (TSCA). TSCA tends to manage a higher level of hazardous material. It’s important to make sure the people handling the waste and management are familiar with TSCA regulations and guidelines.
http://www.epa.gov/epawaste/hazard/tsd/pcbs/pubs/laws.htm
Landfills are also beginning to add disclosure of known PCBs into their screening requirements. So even though there aren’t requirements PCBs are starting to be regulated in other ways.
http://www.epa.gov/epawaste/hazard/tsd/pcbs/pubs/waste.htm
Q. If I do find out if I have PCB caulking or other materials that may contain PCB, what am I required to do with them? In what circumstance would I be required to remove these materials? Do I need to notify local, state or federal regulators of the presence or possible disturbance of these materials?
A: If the material isn’t being disturbed then it needs to be kept it in a good condition. So, for example, if it’s an exposed ledge on an exterior of a building, then it needs to be safely contained.
The EPA is currently conducting an effort to broaden awareness of PCB contamination, health effects as well as guidelines in managing the contaminated material. The biggest focus surrounds schools and maintaining the health and safety of children.
For more on best practices for managing PCB containing materials in schools visit the EPA.
Once PCBs get into soil it isn’t very mobile so it doesn’t migrate too deep but since it doesn’t easily break down it may remain for a long time and potentially cycle between water, air and soil, spreading contamination.
If it’s present in the child’s play area, especially at a shallow level then it is hazardous.
As far as notification, EPA’s requirement is to notify the County and State officials.
It’s important to review workplace risk management procedures for proactive or reactive approach and determine when it is the best time to sample. Be sure to understand if vendors have waste criteria that require PCB identification.
Q. Can my in-house maintenance/engineering staff personnel disturb or clean up PCB contamination? In what circumstance would this be allowed and what training are they required to take?
A: In-house maintenance/ engineering staff would be required to be properly trained on handling and managing the PCB Hazardous Materials. This training is covered in Cal/OSHA’s HAZWOPER trainings.
Q. Where and how are PCB wastes disposed of?
A: All waste should be characterized and analyzed before being shipped to the disposal facility to avoid it being returned.
TCSA regulations state that PCB product waste must be disposed of in one of three ways:
Performance-based disposal: this includes, incineration, disposal in TSCA chemical waste landfill, a RCRA hazardous waste landfill.
Disposal in solid waste landfills: certain waste, such as PCB-containing caulk may be disposed in non-hazardous waste landfills permitted by States. However, EPA recommends that you determine prior to shipment that the landfill is willing and able to accept the PCB waste.
Risk-based option: this allows for a site-specific, risk-based evaluation to determine if waste may be disposed in a manor other than disposal in landfills or performance-based disposal.
For more on waste disposal options, visit http://www.epa.gov.pcbsincaulk/caulkdisposal.htm
Q. What experience do you have addressing EPA guidelines? Any key lessons learned?
A: PCB containing material is something that needs to be identified early on in a project. It’s important to allow plenty of time to deal with the EPA guidelines and develop a strong management plan. It is also imperative to work closely with Labs to make sure they are analyzing as determined by the EPA.
Q. Are there situations where there may be other hazardous materials present in the same materials that contain PCB?
A: Yes, some examples are, Asbestos, Lead, as well as other metals. Soils can have pesticides (chlorine containing compounds) that are based on the same chemistry of PCBs so that can interfere with some of the methods used to detect PCBs.
Other helpful resources: